process

The Process of Jewelry
Bringing something about in the physical world is an age-old challenge. One has an idea, a vision, a sketch of the “real” thing to be made…. and the question arises, how to bring it about? As we know, there is often a chasm between the dream and the reality… as they say, ideas are cheap. Often, while thinking about a certain piece, or to bring together a choice of stones, I make sketches to “try out” different possible approaches. This process is in itself very liberating because the drawing or watercolor can happen so easily and quickly, compared to dealing with expensive three-dimensional materials. When I have an idea of what I want the piece to look like, I have two possible routes to take to translate it into the actual metal. One is the “direct metal” method; the other is the “lost wax” process.
Direct Metal Method
Working metal directly is as old as human history itself… ancient artisans formed pieces of copper, silver, and gold into pieces of astounding beauty, working with very simple tools. What we do today is often very similar in technique to what was done thousands of years ago… and as you may observe by looking at contemporary jewelry, what is done today often lacks the power of the ancient pieces.
The materials used in the making of jewelry, often referred to as “noble”, are remarkable for their resistance to degradation, whether they are the metals of gold or silver, or the natural gemstones formed deep in the earth, with their amazing color, brilliance, and hardness. The most remarkable thing about practicing the art of jewelry making is the simplicity of it all… the senses and strengths of one’s whole body, particularly the hands and eyes, are used to bring about the finished pieces. Bits of metal can be cut, hammered, formed, soldered, engraved and finished in a continuous process, very much as jewelers have done for millennia. However, “simple” is not “easy”…. and I suppose that is the challenge for the craftsman every day in the workshop, to pursue the idea of “perfect” form with the exercise of skill. Needless to say, perfection is never really attained… it is the attempt that matters, and calls us to follow this endless pursuit. I suppose it is the effort to be present to the process and in a sort of “conversation” with the piece as it develops, which is the heart of practicing the art of jewelry making.
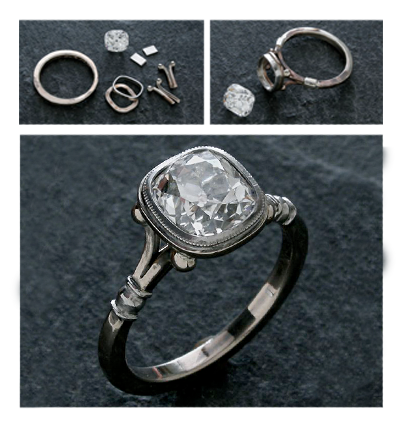
Lost Wax Method
Melting metal and pouring it into a prepared mold is almost as old as direct metalworking itself, about 3000 years. When I work with wax, I form it and model it with my fingers somewhat like working clay…. the wax has a wonderful flexibility, perishability and delicacy very different from the resistant metal. When the wax “model” is finished, it is encased in a plaster mold; then the wax is “burned out” in a kiln, leaving a cavity where model used to be. (Hence the term “lost wax”; the art was never forgotten, but the model itself disappears in the process). Then, the molten metal (18k gold in my case) is poured into the mold, and an amazingly faithful, detailed gold replacement results. Then, the casting– a duplicate of the original wax model– can be finished with abrasives, files, and gravers…. other forged metal pieces may be added, such as bezels to hold the stones, or different metal colors and types.
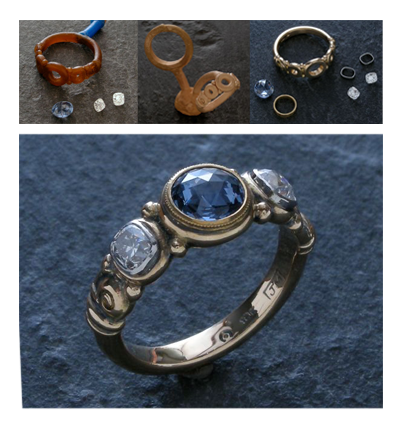